RIM 環太平洋ビジネス情報 1998年7月No.38
グローバル戦略を加速する米国ビッグスリーのアジア展開
1997年07月01日 さくら総合研究所 高安健一、遠山淳子
はじめに
米国の主要完成車メーカーであるビッグスリー(ゼネラル・モーターズ、フォード、クライスラー)は、グローバル戦略を加速するとともに、アジアでの事業展開を活発化している。アジアの自動車産業の現状をみると、アセアンを中心に日本の完成車メーカーが、生産・販売の双方において優位に立っているといえる。しかし、今後、ビッグスリーのアジア戦略が成功を収めるならば、競争が一段と激しさを増し、アジアの自動車産業をめぐる勢力図が変わる可能性がある。
本稿は、ビッグスリーがどのような戦略に基づいてアジアに本格参入しつつあるのかを探るとともに、ビッグスリーのアジア展開が日本の自動車メーカーにどのような影響を及ぼす可能性があるのかを考察するものである。
以下においては、まず、ビッグスリーのグローバル戦略を、それを支える5つの柱という視点から整理する。その後、新興市場攻略の先行事例であるブラジルでの動きを交えながら、タイと上海での事業計画を中心にビッグスリーのアジア戦略を明らかにするととともに、そのアジア展開における課題を考察する。
I.加速するビッグスリーのグローバル戦略
1.北米・欧州(西欧)からアジア・南米へ
ビッグスリーの海外進出の歴史は比較的古い。ゼネラル・モーターズ(GM)は、1918年にカナダの自動車メーカー買収したのち、1910年代を通じて完成車の輸出により、欧州(西欧)・中南米・豪州市場の開拓を進めた。20年代後半からは、英国、ドイツの自動車メーカーを相次いで買収するとともに、世界 15カ国に組み立て工場を建設し、当時、保護主義傾向を強めつつあった欧州を中心に、海外の生産基盤を固めていった。
フォードは、1905年にカナダに工場を建設し、カナダから英国への完成車の輸出により、海外事業を開始した。その後、20年代を通じ、フランス、英国、ドイツ、メキシコ、ニュージーランドなどに子会社を設立し、海外の生産基盤を固めていった。
クライスラーは、30年代以降、欧州、中南米での事業を活発化した。しかし、小型車開発の立ち遅れるなど経営戦略で失敗したため、70年代後半に海外の完全子会社(100%出資子会社)の売却を進め、現地生産を縮小し、北米、メキシコからの輸出を中心とする海外への供給体制に転換した。
最近のビッグスリーの海外での地域別販売台数をみると、GMとフォードは欧州が、クライスラーはカナダ、メキシコが多い。このように、ビッグスリーの海外における事業展開は、北米、欧州を中心に進められてきた(表1)。
アジア地域については、70年代に入ってから、日本、台湾、韓国を中心に進出したものの、日本メーカーや現地メーカーとの競合により、市場シェアは伸び悩んでいる。
ビッグスリーが今後、長期にわたってグローバル企業として成長し続けていくためには、新興市場を含む世界市場でシェアを拡大し、収益を確保していくことが不可欠である。ビッグスリーは北米、欧州の自動車市場が成熟し、今後、大きな成長が望めないことから、アジア、南米、東欧などの新興市場に注目している。ビッグスリーは、特に、急速な経済発展を背景に購買力が高まっているアジアを、世界で最も成長性の高い市場として位置づけている。
GMは2006年までにアジア・太平洋地域での市場シェアを10%に(現在5%)、フォードは2000年までに、自社の販売台数に占めるアジアのシェアを 15~20%に(現在2.5%以下)、クライスラーは2000年までにアジアを含む海外での販売台数を30万台(現在22万台)にする計画をそれぞれ明らかにしている。
2.グローバル戦略を支える5つの柱
ビッグスリーのグローバル戦略の狙いは、自動車の製造方法をグローバル規模で再構築することと、各地域の市場特性に適した自動車を低価格で供給することを両立させることによる、世界市場でのシェア拡大である。
ビッグスリーがこのようなグローバル戦略に取り組むのは、今回が初めてではない。GMは70年代に、世界各国のGM関連サプライヤーが生産を分担した主要部品を使い、世界各国の工場で小型車を生産することにより、規模の経済性を最大限に発揮することを狙った「ワールド・カー」構想を打ち出し、80年代初頭にアジア市場に投入した。しかし、販売実績は期待を大幅に下回り、撤退を余儀なくされた。
90年代中頃になると、ビッグスリーは相次いで新たなグローバル戦略を打ち出した。なかでもフォードは、94年4月に中長期経営計画である「フォード2000」プロジェクトを発表し、市場シェアの拡大目標や地域別事業部の統合計画などを明確にした。
ビッグスリーのグローバル戦略の成否の鍵を握るのが、(1)プラットフォームの共通化(注1)、(2)部品のシステム化・モジュール化(注2)、(3)サプライヤーによるQS9000の取得(注3)、(4)エレクトロニクス技術の応用(注4)、(5)情報通信ネットワークの活用(注5)、である(図1)。
互いに密接な関係にあるこれらの5つの柱を同時に推進することが、グローバル規模での効率的な生産、供給の実現に欠かせない。
まず、共通プラットフォームの開発については、システム化・モジュール化された部品を組み付けることを前提に、サプライヤーが設計段階から参加する必要がある。部品のシステム化・モジュール化に際しては、高度な開発・設計能力、技術力、管理能力が求められるため、QS9000を取得するなど、サプライヤーは品質管理に関して信頼のおける存在であることを求められる。また、部品のシステム化・モジュール化にはエレクトロニクス技術の応用が不可欠である。そして、このように複雑化する製造工程を、正確かつ迅速に進めるためには、開発部門、組み立て部門、サプライヤーなどが情報通信ネットワークで結ばれ、情報交換が円滑に行われる必要がある。
このようなシナジー効果が発揮されれば、開発期間の短縮、製造コストの削減、車種の多様化、品質の向上・安定化が可能となるのみならず、市場のニーズに適した、価格競争力のある自動車を供給できるようになると考えられる。
これら5つの柱に基づく新たな自動車の製造方法は、いまや世界的な潮流となっている。日本の完成車メーカーもこれらに取り組み始めているが、現状では、ビッグスリーの方が先行しているといえよう。
II.活発化するビッグスリーのアジア展開
1.アジアにおける完成車メーカーの勢力図
アジアの自動車産業の現状をみると、アセアンを中心に日本の完成車メーカーが生産、販売の双方において大きなシェアを占めている一方、中国、インドでは、欧米メーカーが積極的に事業を展開している。このようなアジアの自動車産業の勢力図は、今後、ビッグスリーのグローバル戦略・アジア戦略を反映して微妙に変化してくる可能性がある。
(1) アセアン
日本の完成車メーカーは60年代からアセアンに進出し、各国政府の国産化政策などに対応しつつ、生産基盤を着々と築いてきた。その結果、今日では、アセアンの自動車産業における日本メーカーのシェアは、生産で90.5%、販売で91.7%と極めて高い水準となっている(表3)。
表3 アジアにおけるメーカー別自動車生産・販売状況(1995年)
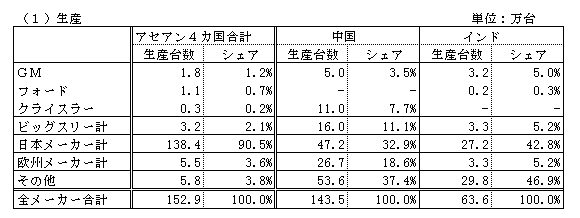
(資料)FOURIN「1995/1996アジア自動車産業」、日本自動車工業会「主要国自動車統計」よりさくら総合研究所作成
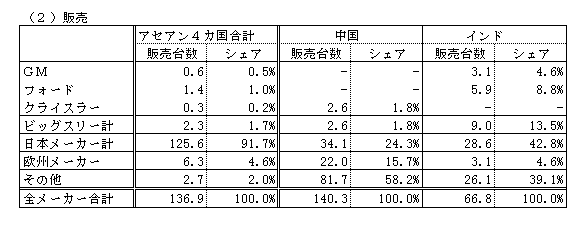
(資料)FOURIN「1995/1996アジア自動車産業」、大和総合研究所「Singapore Market Review & Outlook 4Q96」(原典:各国自動車工業会資料)よりさくら総合研究所作成
しかし、最近は、高級車市場に的を絞る欧州メーカーや、低価格車の投入により市場拡大を図る韓国メーカーがアセアンで活発な動きをみせている。
また、マレーシアでは、国民車メーカーであるプロトン社が市場の3分の2近くを占めている。ベトナムでは、政府が外資系企業の進出を次々と認可したため、市場規模が2万台程度と小さいにもかかわらず、日・欧・米・韓メーカーが激しいシェア獲得競争を展開している。
(2) 中国
中国では、80年代に「改革・開放」路線の下で資本の自由化が推進されると、外資との提携により競争力強化を図る地場の自動車メーカーが多数現われた。それらの地場メーカーは、資金の確保および技術の導入を目的として外国の完成車メーカーとの合弁を進めたため、この時期に日・欧・米の完成車メーカーの中国進出が進展した。
しかし、大小様々な自動車メーカーが行政系統によって分断された別々の市場で、開発から生産までを個々に行っていたため、量産体制の確立と技術発展には至らなかった。
こうした背景から、中国政府は89年から92年にかけて、乗用車生産を8社に集約させる「三大三小二微」体制を導入し、国内乗用車メーカーの保護育成を目指した。
この過程で、中国の自動車産業(乗用車)において、欧州完成車メーカーが圧倒的な勢力を持つようになった。これは、「三大」メーカーがいずれも欧州メーカー(フォルクスワーゲン、シトロエン)と合弁しているのに対し、米国メーカーの合弁相手は「三小」のうちの2社、日本メーカーの合弁相手が「三小」のうちの1社と「二微」にとどまっていることからもうかがえる。
(3) インド
インドでは、83年に日本のスズキとインド政府との合弁であるマルチ・ウドヨグ社(以下、マルチ社)が小型乗用車生産を開始して以来、マルチ社が圧倒的な市場シェアを維持している。
93年に乗用車製造部門への外資参入規制が緩和されると、欧米や韓国の自動車メーカーが相次いでインドに進出したが、マルチ社は依然として70%以上の市場シェアを保っている。
スズキの進出以降、日本メーカーでは目立った動きはなかったが、97年秋から本田がアジア戦略車「シティ」の生産を、99年からトヨタが乗用車生産をそれぞれ開始する予定である。
2.ビッグスリーのアジア戦略
このように現状では、ビッグスリーのアジア市場でのプレゼンスは小さいといえる。その理由は数多く挙げられようが、その1つに小型車の開発・生産を苦手としていたことがある。
アジアの自動車市場は商用車中心の市場ではあるが、近年、都市部に住む共働き世帯などを中心に、燃費がよく、価格帯が低い小型乗用車に対する需要が高まっている。今後、経済成長を反映して、小型乗用車への需要がさらに高まると見込まれることに加え、消費者の自動車に対する志向が多様化すると予想される。
ビッグスリーがアジア市場に食い込むためには、小型車の投入が不可欠である。しかし、小型車の生産は、一定の生産量を確保し、規模の経済性を発揮しないと十分な利益を得られない。このため、ビッグスリーはアジア市場のニーズに適した低価格帯の小型車を、欧州・日本市場への供給と連動させながら、グローバル規模で生産しようとしている。
ビッグスリーのアジア戦略は、次のように整理できよう。
第一は、ビッグスリーが長期的な視点から、アジア市場の開拓を進めようとしていることである。ビッグスリーは、近年、米国本土での順調な業績を背景に、大規模な海外投資を行う体力を備えており、長期的な視点からのアジア投資が可能となっている。
第二は、世界に保有している経営資源を活用することにより、事業立ち上げに要する期間の短縮・省力化を図っていることである。その例として、GMが欧州のオペル車をベースにした小型乗用車をアジアで生産・供給したり、フォードがマツダとの提携により、マツダの資本や技術に加え、そのアジア・ネットワークを活用しようとしていることが指摘できる。
第三は、日本メーカーと比較して、1拠点当たりの生産規模が大きいことである。GMはタイで15万台、上海で10万台、フォードはタイで13万5,000 台規模の生産能力を持つ工場を建設している。また、ビッグスリーの中では海外生産規模が小さいクライスラーも、中国の工場における「チェロキー」、オフロード車の生産を2003年に20万台に乗せる計画である。日本の完成車メーカーの場合、アジア域内の拠点数は多いものの、年産10万台を越える拠点は 10ヵ所に満たない。
このような生産規模の違いは、日本メーカーが当初、輸出代替を目的として各国へ進出したのに対し、ビッグスリーは貿易自由化の進展をにらんで、当初から域内全体を一つの市場としてみているところに起因するといえよう。
第四は、ビッグスリーが工場の立ち上げ時点からアジア域内外への輸出(GMが80%、フォードが約50%)を計画していることである。アジアの拠点を、世界への小型車供給基地として活用しようとするビッグスリーの意図がうかがえる。
第五は、ビッグスリーは小型車に加え、右ハンドル車やオフロード車など、市場の多様なニーズに適した自動車を生産、供給してきていることである。
3.注目されるタイ、上海での事業計画
最近のビッグスリーのアジア戦略の中で、特に注目されるのが、タイ、上海での事業計画である。
(1) タイ
GMとフォードは、アジアにおける大規模な自動車生産・輸出基地として、タイを選んだ。タイはアセアン最大の自動車市場(約57万台、96年)を有し、日本メーカーを中心に、海外から多数の完成車メーカーが進出している。このため、サポーティング産業やインフラ、人材などの産業基盤の整備が他のアセアン諸国よりも進んでおり、完成車メーカーにとっては、生産体制を整えやすい。
GMは7億5,000万米ドルを投じ、99年からオペル車をベースとした小型乗用車の生産を開始する。GMは、タイで生産する小型乗用車15万台のうち 80%を日本、豪州、アジア域内へ輸出する計画である。また、GMは生産開始に先立ち、自動車ローン会社の設立や、人材育成センターの開設を打ち出しており、タイをアセアンの生産・輸出基地として位置づけ、ソフト面の整備にも力を入れている。
一方、フォードは、98年からタイでピックアップトラックの生産を開始し、年間生産台数13万5,000台のうち半数以上を米国以外の海外市場に輸出する計画である。部品の調達については、マツダのアジア・ネットワークを活用するなどして、現地調達率を52%以上にする予定である。
(2) 上海
GMは上海でも大規模プロジェクトを進めている。GMは、巨大な潜在需要を抱える中国市場を重視しており、現地で生産工場を立ち上げることによって、着実に市場を獲得することを狙っている。GMの上海における事業は、総投資額が15億7,000万米ドルに上る、米中両国間で最大の合弁プロジェクトである。
上海でのプロジェクトには、GMのほか、フォード、トヨタも参画を狙っていたが、97年3月にGMと上海汽車工業総公司との合弁が決定した。GMは98年より「ビュイック」シリーズの中高級乗用車を年間10万台生産し、うち30%を輸出する予定である。現地調達率は3年間で80%まで引き上げられる見込みである。市場のニーズに適した自動車を開発するため、300人の開発部隊を上海に常駐させるとの報道もある。
また、生産工場の立ち上げと同時に、汎アジア自動車技術センターを設立し、自動車部品のエンジニアリング施設、専門技術の研修施設として、中国国外へのサービスも進める計画である。
このようなGMの積極的な取り組みとは対照的に、日本や欧州メーカーの中には、中国での自動車生産事業から撤退する動きもみられる。近年撤退を決めたある完成車メーカーは、高い経済成長率の割に国民の購買力が高まらず、期待していたよりも市場拡大ペースが遅いと判断したことを理由として挙げている。
4.鍵を握る主要サプライヤーの動き
ビッグスリーのアジア戦略の成否の鍵を握る最大の要因は、自動車製造コストの8割以上を占める部品の供給である。
GMとフォードは、アジアでの生産増強に際し、主要サプライヤーに協力を要請している。ビッグスリーがアジアでの事業展開において、どの程度プラットフォームの共通化や部品のシステム化・モジュール化を取り入れるかはまだ公表されていない。しかし、アジアをグローバル戦略の一環として位置づけていることから、ビッグスリーがそれらを取り入れてくる可能性は十分にあろう。すでにいくつかのサプライヤーが、アジアでモジュール部品を供給する計画を発表している。
世界最大の自動車部品サプライヤーであるGM系列のデルファイ・オートモーティブ・システムズ(以下、デルファイ)は、98年をめどにタイでブレーキやステアリング、冷却・空調システムなどの主要なシステム部品・モジュール部品の生産を開始する。99年にタイで自動車生産を開始するGMへの供給のほか、トヨタなど日本メーカーへの売り込みも図る構えである。また、デルファイは、上海でも現地の部品メーカーに最新の製品である前輪キャリパーブレーキの技術を供与し、上海のGMへ供給するとも発表している。
一方、フォードにかかわるサプライヤーの動きでは、システム部品・モジュール部品関連の情報はまだないが、アセアンでの実績を持つ日本のマツダ系電装品メーカー(ユーシン)がフォードからキーセット(イグニッションキー、ドアロック、トランクキーから成る)の受注を獲得し、増産体制の整備を進めているという。
5.先行事例としてのブラジル
ビッグスリーは、タイや中国(上海)の主力工場での生産開始を98年以降に予定しており、現時点では、まだ生産を行っていない。ビッグスリーのアジア展開を展望する際の参考として、ここでは、ビッグスリーがグローバル戦略と新興市場戦略を連動させているブラジルのケースを先行事例として紹介する。
南米は経済パフォーマンスの好転、とりわけインフレの鎮静化を受けて、自動車購入意欲が高まっており、アジアと並ぶ成長市場として注目されている。
ブラジルの自動車市場規模は南米最大であり、95年に172万台に達した。これは同年のアセアン(主要4カ国計137万台)、中国(140万台)、インド(62万台)を上回るものである。市場規模は2000年には200万台に達すると見込まれている。
ブラジル、アルゼンチン、ウルグアイ、パラグアイで構成される自由貿易圏であるメルコスル(南部南米共同市場)が、他の南米諸国や欧州にも拡大する動きもあり、完成車メーカーによる南米への投資が活発化している。
欧米の完成車メーカーは、すでにブラジルを中心に低価格車を投入しており、熾烈な市場獲得競争を繰り広げている(表6)。イタリアのフィアット社が1万460米ドルの低価格乗用車を96年に約20万台販売し、実績を上げているのがその一例である。
ビッグスリーも小型乗用車の生産・販売に力を入れており、フォードが97年3月に、1万米ドルの小型乗用車「Ka」の販売を開始したほか、GMが99年から9,000米ドルを切る低価格乗用車の生産を開始する計画を発表している。
ブラジルでのGMの事業展開に関し、特に注目されるのは、(1)1拠点当たりの生産台数が極めて大きいこと、(2)部品のシステム化・モジュール化を取り入れていく方針であること、の2点である。小型車の場合、利益を確保するためには量産効果を上げる必要があるので、GMはブラジルの工場で生産する乗用車を南米域内外へ輸出することを前提に、年産100万台の生産計画を立てている。
部品のシステム化・モジュール化に関しては、独のフォルクスワーゲン(VW)社がすでにブラジル工場で取り入れて成功させた事例がある。
VW社は、組み立てラインに沿って部品メーカーがシステム化・モジュール化した部品を組み付ける生産システム「モジュール・コンソーシアム(区割りされた企業連合)」を導入し、ラインでの作業の省力化と製造のコスト削減を実現している。GMも同様な生産方式を取り入れ、コスト削減につなげる計画であると伝えられている。
6.ビッグスリーの課題
ビッグスリーのグローバル戦略は、自動車の生産・供給システムを根本から変えることによって競争力の向上を図ろうとするものである。アジアでの本格的な事業展開に際しても、ビッグスリーが先述の5つの柱を有効に活用しながら、競争力のある自動車の生産を推進してくることが十分に予想される。
しかし、ビッグスリーがアジア市場に食い込むためには、自動車の製造方法はもちろんのこと、販売・マーケティングなどの側面で克服しなければならない課題が多く残されている。
第一の課題は、すでに述べたように、部品の調達、とりわけ一次サプライヤーの協力がどの程度得られるかという点である。
第二は、アジアでの販売実績が少ないビッグスリーが、いかにしてブランドイメージを作り上げていくかという点である。日本を含むアジアでは、日本車や欧州車は高いブランド力を持っている。ちなみに、ビッグスリーが日本で長年にわたって苦戦を強いられてきた理由の1つに、ブランド力の弱さが挙げられよう。
第三は、ビッグスリーが販売・サービス網を充実させることができるかという点である。日本車がアジアで圧倒的なシェアを占めている背景として、ブランドイメージ、高い技術力に加え、充実した販売・サービス網の存在がある。
第四は、アジアでの1カ国・1工場当たりの生産規模が小さい点である。先に触れたブラジルの例では、GMの販売台数は約35万台(96年)であり、投資額は95~2000年に20億米ドルに達する。投資規模と生産規模が拡大するほど、一次サプライヤーの進出が促進され、完成車メーカーはシステム化・モジュール化された部品の供給を受ける余地が大きくなる。
ブラジルの工場と比較すると、アジアの場合、生産規模がさほど大きくない。稼働率を高めて量産効果を発揮させるためには、工場立ち上げ当初より輸出を行い、生産台数を確保しなければならない。ところが、アセアン諸国の自動車部門の貿易収支をみると、すでに大幅な赤字を計上しており、域内輸出が円滑に進む保証はない。アセアン域内の製品・部品の相互供給の促進を狙って、96年11月に導入されたアセアン産業協力協定(AICO)スキームは、アセアン各国の足並みが揃わず、いまだ適用事例がない。
第五は、新工場が立ち上がり、生産・輸出を開始する前に、主力工場が位置するタイと中国の自動車販売が調整局面を迎えたことである。現在、タイでは自動車市場の落ち込みが顕著になりつつある。アセアン地域でも供給過剰への懸念が出始めている中で、いかにして販売先を確保するのかといった問題がある。
表7 ビッグスリーと日本の完成車メーカーのアジアにおける事業展開の比較(アセアンの場合)
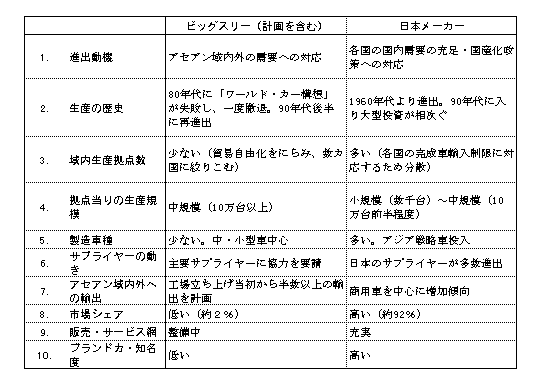
(資料)各種資料よりさくら総合研究所作成
おわりに
日本の自動車産業は、今後、ビッグスリーのアジア展開に対し、これまで以上に関心を払う必要があろう。
まず、日本の完成車メーカーにとっては、アジアの自動車市場をめぐってビッグスリーとの間で競争が激化する可能性がある。現在、日本の完成車メーカーはアジアにおいて、需要が旺盛なピックアップトラック市場で優位を保っている。今後の成長が見込まれる小型乗用車市場においても、欧米メーカーに先駆けてアジア戦略車を投入し、着実にシェアを伸ばしている。
しかし、ビッグスリーの新工場が稼動し、供給が開始される98年以降、タイと上海だけでもビッグスリー3社合計で50万台近く供給量が増えることになる。
また、ビッグスリーと日本の完成車メーカーは、アジアでの事業展開に際し、製造コストの削減と市場のニーズに適した自動車の供給を目指している点で軌を一にしているが、アジア戦略とグローバル戦略との連動という点ではビッグスリーの方がより密接であるように思われる。
ビッグスリーのグローバル戦略は、北米、欧州、中南米では軌道に乗り始めており、98年以降、アジアの新工場が稼動すれば、グローバル規模での供給体制が整うことになる。これに対し、日本の完成車メーカーは、国内外において、プラットフォームの共通化、部品のシステム化・ネットワーク化、品質管理の徹底、エレクトロニクス技術の応用、情報通信ネットワークの活用などを推進してはいるものの、明確なグローバル戦略が打ち出されているようには思われず、アジア戦略との関係もみえてこない。
ビッグスリーとの競合に備え、日本の完成車メーカーにも明確なグローバル戦略の構築とその中におけるアジア戦略の位置づけが求められる。
他方、日本のサプライヤーにとっては、ビッグスリーによるアジアでの生産増強はビジネス・チャンスの拡大につながろう。かつて、日本の完成車メーカーの対米進出支援のために米国進出に踏み切った日本のサプライヤーが、最近、米国でビッグスリーから大規模な受注を獲得するケースが増えている。
ビッグスリーへの部品供給の実績が評価されれば、米国国内だけでなく、アジアを含めた海外の工場へ部品を供給する可能性も高まろう。ビッグスリーに対する部品の供給実績を着実に積み、かつアセアンを中心に多くの拠点を持つ日本のサプライヤーの対応が注目される。
これまで日本の完成車メーカー、サプライヤーともに、アジアでの事業を推進する際に、ビッグスリーの存在を強く意識することは少なかったように思われる。しかしながら、アジア市場においても、ビッグスリーが、日本の完成車メーカーにとってはタフな競争相手、サプライヤーにとっては新たな製品の納入先として浮上してくる可能性がある。今後数年間、ビッグスリーのアジア展開の行方が注目されるとともに、本格的な競争時代を生き抜くための日本の自動車メーカーの戦略が問われることになろう。
注
1. プラットフォームとは、床構造にエンジンルーム、変速機、車軸など駆動計部品を加えた車輌の土台にあたる部分のことである。総額数百億円~一千億円を要するといわれている新型車の開発コストのうち、およそ3分の2を占めるのがプラットフォームの開発コストであるといわれている。したがって、その開発コストを削減するとともに、1つのプラットフォームからどれだけ多様な自動車を開発できるかが、開発コスト削減の最大の鍵を握る。ビッグスリー各社の取り組み状況をみると、GMは2005年をめどにプラットフォームの数を7(現行14)に絞り、1プラットフォーム当たり最低100万台を生産し、数億米ドルのコスト削減を図るとしている。フォードは、プラットフォームの数を2005年までに16(現行24)に減らす一方で、1プラットフォームあたりのモデル数を8モデル(現行5モデル)に拡大するとしている。クライスラーは2000年までにプラットフォームの数を7~8に統合する計画である。
2. 部品のシステム化・モジュール化とは、サプライヤーが部品をより大きな部品単位に組み上げて完成車メーカーに納入することにより、部品点数の削減、部品製造工程でのコスト削減、最終組み立て工程の簡素化、組み立て期間の短縮化、品質の安定化を実現するものである。完成車メーカーから、システム部品・モジュール部品を供給する一次サプライヤーに指定されると、そのサプライヤーは大量の受注を確保することができる。一次サプライヤーとなるには、完成車メーカーによるプラットフォームの設計段階から開発・設計に参加できる能力が求められるとともに、自社に部品を供給する二次・三次サプライヤーに対する管理能力が問われる。こうした背景から、ビッグスリーは一次サプライヤーの絞り込みを行っている。すでにビッグスリーはサプライヤーに対し、部品をシステム化・モジュール化して納入することを要請しており、サプライヤー側も自助努力や他企業との提携などにより対応している。ビッグスリーがグローバル戦略に基づいて部品のシステム化・モジュール化を推進する中で、一次サプライヤーとしての地位を確保しようとするサプライヤーは、グローバル規模でシステム部品・モジュール部品を供給できる体制を整備することを求められることになろう(グローバル・サプライヤー化)。
3. 「QS9000」とは、ビッグスリーおよびトラック業界(5社)が自動車部品・資材供給者に対する品質システムの要求基準として、「ISO9001」をベースに、自動車業界特有の要求事項を付加した共通品質システム規格である。QS9000の取得により、品質改善やコスト削減といった効果が期待できる。Automotive Industry Action Groupの調査によれば、米国ではすでに、1,100~1,200の工場・事業所等がQS9000を取得しており、これにより米国の自動車業界全体で、 24億米ドルのコスト削減効果が生じたと推測されている。QS9000の取得が、ビッグスリーがサプライヤーを絞り込む際の基準の1つになっているといわれている。
4. ビッグスリーに限らず、自動車産業が成立するためには、エレクトロニクス技術はなくてはならない存在となっている。近年、自動車の安全性に対する要求や、地球規模での環境意識が高まるのに伴い、自動車産業におけるエレクトロニクス技術へのニーズはさらに高まっている。自動車メーカーによる一般的な取り組みとしては、安全対策分野では、乗員の有無や姿勢等に応じて作動するエアバッグ・システム、路面状況や運転状態に合わせたサスペンション・システム、電子制御パワーステアリングなどの開発・改良が進められている。また、環境対策分野では、エンジン、変速機を始めとした駆動・伝動系部位を電子制御することにより、排気ガスや振動、騒音などを低減させる技術の開発・改良が進められている。
5. 情報通信ネットワークは、自動車の設計、製造、販売など広い範囲で利用され、作業の円滑化、省力化、期間の短縮化に貢献している。ビッグスリーもその整備に積極的に取り組んでおり、サプライヤーとの間で部品情報を交換しているほか、設計部門と本社、設計部門と現地生産拠点との間では、CAD/CAMを用いて図面データの交換などを積極的に行っている。さらにビッグスリーは、現在、企業ごとに異なっている通信手法をインターネット対応のEDIに標準化し、米国の自動車産業界全体をカバーする大規模ネットワークの構築をする計画に参加している。このようなシステムの導入は、サプライヤーによる複数のメーカーとの取引を円滑にし、経営の効率化につながると期待されている。
主要参考文献
1. FOURIN「1995 北米自動車産業」
2. FOURIN「1995/1996 アジア自動車産業」
3. FOURIN「自動車調査月報」各月号
4. 日刊自動車新聞車『自動産業ハンドブック』1997年
5. 下川浩一「自動車、調達戦略で米と一線」(日本経済新聞「経済教室」1996年3月19日)
6. 井上昭一『GMの研究―アメリカ自動車経営史』ミネルヴァ書房、1982年
7. さくら総合研究所環太平洋研究センター『競争時代を迎える東南アジア地域の自動車産業』(RIM34号 1996年7月 所収)
8. 遠山淳子「競争力向上に取り組むアセアン自動車産業」(日本自動車工業会『JAMAGAZINE』 1997年6月号)
9. General Motors Corporation,1996 Annual Report
10. Ford Motor Company,1995 Annual Report
11. Ward's Communications, Ward's Automotive Report 各号
12. Ward's Communications, 1996 Ward's Automotive Yearbook
13. Chrysler Corporation, Ford Motor Company and General Motors Corporation, Quality System Requirements QS9000 International Organization for Standardization, August 1994.
14. "Creating the Best CAD/CAM System" in Automotive Industry December 1996.
15. "Danger: Rough Road Ahead" in Fortune, March 17, 1997.
16. GM、ホームページ http://www.gm.com
17. フォード、ホームページ http://www.ford.com
18. クライスラー、ホームページ http://www.media.chrysler.com