コラム「研究員のココロ」
生産リードタイムはどこまで短くできるのだろう?
2006年04月10日 松崎健一
前回(第1回:どうして生産管理は難しいの?)は、生産を行進中の兵士の隊列にたとえて、TOC(Theory Of Constraints:制約条件の理論)による生産革新の手法であるDBR(Drum-Buffer-Rope:ドラム・バッファ・ロープ)を紹介しました。今回は、TOC/DBR導入による代表的な効果である、生産リードタイムの極小化について、どのようなメカニズムでその効果が出るのかを事例も交えながら紹介しましょう。
1.生産リードタイムは簡単に短くできる?
TOC/DBRによる想定効果としてまず挙げられるのは、生産リードタイムが極小化されることです。また、その生産リードタイムの短縮に比例して仕掛り量も削減されますし、その仕掛りを置くポイントも絞り込まれます。しかし、多くの工場で、現状は、仕掛りが工程間で大量に積み上がっていることがよく見受けられます。仕掛りが多くなれば、それだけ工程間で滞留している時間が長くなるので、投入から出荷までの生産リードタイムは長くなってしまいます。
TOC/DBRでは、ドラム工程と出荷工程の前だけに若干の仕掛りを置いてあげます。それにより、生産リードタイムを極小化します。では、多くの工場で、なぜ工程間に仕掛りを多く持っているのでしょうか?従業員のみなさんが、生産リードタイムを長くしてやろうと思って、仕掛りを溜め込んでいるのでしょうか?まさかそんな悪意を持った従業員の方はいらっしゃいません。
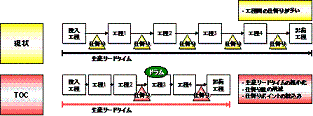
2.生産性を上げようとしたら生産リードタイムが長くなっちゃった
従業員のみなさんは評価指標にしたがって行動しています。多くの工場では、各工程の生産性(たとえば稼働率や時間当たり生産量など)という指標によって評価されているために、各工程の担当者は、自分の工程に都合の良いように、順序を入れ替えたり、まとめて生産したりしようとします。すると、そうするためには、自分の工程の前に仕掛りを持っておかなければならなくなりますし、まとめて生産されたものは次の工程の前で大量に仕掛かってしまうことになるのです。結果として、各工程の生産性を上げようとしたために、生産リードタイムを長くしてしまうという悲劇が生じるわけです。
たとえば、電子部品を製造しているある工場では、従来、生産リードタイムが20日程度でした。ところが、TOC/DBRを導入してみると5分の1の4日程度に短縮できました。導入時に工程を詳しく分析してみると、正味の処理時間の合計は約2日でした。ということは、残りの約18日は工程間に滞留していただけなのです。
この工場では、従業員一人あたりの生産性を第一の管理指標としていたため、各工程で手待ちが生じるのは良くないこととされ、手待ちが生じると、明日使うかもしれない、または明後日使うかもしれない仕掛り品を作っておくという行動を取っていたのです(そのような仕掛り品の多くは明々後日になっても使われなかったりするのですが...)。また、各工程の生産性を管理指標としていたため、すべての工程を厳しく等しく管理し、各工程が効率追求の観点から自分の工程に都合の良いスケジュールを策定していました。
この工場の工程数は20程度でしたから、各工程間に1日分ずつの仕掛りを持ってしまうと、簡単に20日分くらいの仕掛りを工場全体で抱えてしまうわけです。たとえ各工程の生産性(たとえば稼働率)が高まったとしても、工場全体の生産リードタイムが長くなって競争力を落としてしまっていては、まったく意味がありません。ただし、ドラム工程に限っては、稼働率を高めなければならないというのは正しいことですから、ドラム工程の稼働率は指標として管理するのが良いでしょう。
そこで、TOC/DBR導入後は、工場全体のスループットと納期遵守率を管理指標とするように変更しました。そうすると、ドラム工程での手待ちは良くないので、ドラム工程の前だけにはバッファを作り、そのバッファを管理することになります。また、すべての工程を厳しく等しく管理するのではなく、ドラム工程のみを管理し、その他の工程はドラム工程のペースに従うようにしました。その結果、正味の処理時間の合計である約2日に、ドラム工程の前のバッファ1日と出荷工程の前のバッファ1日を足して、生産リードタイムが約4日となり、導入前の5分の1に短縮されたのです。
3.方針と評価指標を変えなくっちゃ!
今でも多くの工場や会社では、遊んでいる(手待ちの)設備や従業員なんて浪費の最たるものだ、という従来の考えにもとづいて業務が運営されています。工場や会社はしばしば“チェーン”にたとえられます。いくつもの工程や機能という”鎖の輪”がつながって、工場や会社という“チェーン”が構成されているという意味です。従来の考えでは、どの“鎖の輪”にも重量があり、だからこそ“チェーン”のどの“鎖の輪”を改善(軽量化)しても、それは“チェーン”全体の改善(軽量化)とみなします。すなわち、部分改善の総和は全体改善に等しいと考えます。

でも、果たしてそうでしょうか?それでは、“チェーン”の強度を決定しているものは何でしょうか?それは、もっとも弱い“鎖の輪”であり、“チェーン”の強さは一番弱い“鎖の輪”の強さと等しいのです。だからこそ、すべての“鎖の輪”を強化したとしても、“チェーン”全体のパフォーマンスは改善されないのです。すなわち、部分改善の総和は全体改善に等しくないのです。

TOC/DBRでは、部分改善の総和は全体改善に等しくないという考えにもとづき、全体最適の観点から、もっとも弱い“鎖の輪”であるドラム工程を徹底活用して強化し、“チェーン”である工場全体の競争力を強化するという変革を起こします。
でも、その際に注意しなければならないのは、初めにも申し上げたとおり、従業員のみなさんは評価指標にしたがって行動しているということです。工場や会社の方針が評価指標を規定し、その評価指標が従業員のみなさんの行動を誘発するのです。本当に変革を起こそうと思えば、従業員のみなさんに行動を変えてもらわなければいけないわけですから、そのためには、工場や会社の方針と評価指標を変えきることが非常に重要です。自力でTOC/DBRを導入しようとして頓挫している理由の一つに、評価指標を変えきれなかったことがあげられるようです。
4.ところでどれくらい生産リードタイムは短くなるの?
前回にも申し上げましたとおり、我々の経験では、生産リードタイム短縮や仕掛り削減で5割以上の改善も珍しくありません。簡単に言うと、TOC/DBRはすべてのオーダーを緊急オーダー(特急品)と同じスピードで生産することを目指しますし実現します。したがって、自社における、生産リードタイムの実績値の平均と、緊急オーダーの生産リードタイムの差が、TOC/DBRによるおおよその改善機会と考えればよいでしょう。厳密に言うと、そこから若干のバッファを考慮して差し引いてあげなければなりません。
なお、TOC/DBR導入にあたっては、生産リードタイムの短縮や、次回に詳しく説明する生産能力の向上などが、自社にとって競争力の向上に寄与するのかどうか、すなわち結果としてスループット向上につながるのかどうかが、導入すべきかどうかの判断基準となります。
また、TOC/DBRを導入した多くの工場で、自社内の生産という機能において、生産リードタイムの短縮などの効果を出すと、制約条件が他の機能に移っていきます。たとえば、サプライヤーからの原材料の調達であったり、協力会社(外注)からの半製品の送り込み・受け入れであったり、顧客からの受注といった他の機能が新たな制約条件となるのです。単に工場内の制約工程が変化していくのに注意を払うだけではなく、外部に移った制約条件にも対処していく必要があります。
ちなみに、サプライヤーや協力会社(外注)に制約条件が移った場合の対処方法としては、先方にもTOC/DBRを導入してもらって生産リードタイムを短くしたり、自社と先方との間を実需に基づいた補充の仕組みに変革したりすることが考えられます。実需に基づいた補充の仕組みを企業間サプライチェーンに導入するってどういうことかに興味がおありの方は、ゴールドラットが書いた『ザ・ゴール2』(原題:It’s Not Luck)を読まれることをお勧めします。これも『ザ・ゴール』と同様に小説仕立てとなっています。また、この本の中ではTOCベースのサプライチェーン・マネジメントだけではなく、TOCの根幹とも言える思考プロセス(Thinking Process)も紹介されていますので、一読の価値ありです。
それでは、次回は、生産リードタイム短縮・仕掛り量削減と並んで、TOC/DBR導入による代表的な効果である生産能力向上について、また事例も交えて説明したいと思います。
第1回:どうして生産管理は難しいの?
第2回:生産リードタイムはどこまで短くできるのだろう?
第3回:設備投資なしで生産能力が増えるってホント?
第4回:TOCとJITって仲良し?仲悪い?
以 上