コラム「研究員のココロ」
どうして生産管理は難しいの?
2006年04月03日 松崎健一
計4回の連載を通じて、我々が取り組んでいる、TOC(Theory Of Constraints:制約条件の理論)による生産革新について、事例を交えながら紹介していきたいと思います。第1回ではTOCの概要とTOCによる生産革新の概要を紹介しましょう。
1.どうして生産管理は難しいの?
そもそも、どうして生産を管理するのは難しいのでしょうか?これまで多くのメーカーの工場を訪れて、工場を見学したり、工場のみなさんから話を聞いてきた中で、よく目にしたり耳にしたのは次のような10個の理由でした。
- 納期遅れが頻発する
- 残業が余りにも多い
- 当初の計画が非常に短期間で変更される
- 優先順位が常に変動する
- 顧客の緊急オーダーに対応できない
- 原材料・部品の不足が頻発する
- 督促が余りにも多い
- 生産リードタイムが非常に長い
- 仕掛り品・原材料在庫レベルが非常に高い
- 現在の生産管理の仕組みでは、どこでどれだけの在庫を持てば良いのか分からない
どうでしょう?みなさんの工場や会社でも当てはまるものがあるでしょうか?このような質問をすると、多くの方が『8個くらいは当てはまるかなあ』『10個すべて当てはまっているよ』『まるでうちの会社のことのようだ』とおっしゃいますがし、ある社長さんには『こんなものは永遠の経営課題であって、なくならないものなんだよ』と怒られたりもします。
日本の製造業の競争力は高いとよく言われますが、このような苦労をしながらも、現場力で何とかその高い競争力を保っているのが実情でないかと感じます。我々は、現場のみなさんが、このような苦労から解放され、もう少し楽に(シンプルに)生産を管理し、競争力の更なる向上に挑んでもらいたいという思いで、TOC(Theory Of Constraints:制約条件の理論)に取り組んでいます。
2.TOCって?
まず初めに、TOCという理論がどのようなものかを紹介しましょう。TOCは、日本でもベストセラーとなった『The Goal』(邦題:ザ・ゴール)、『It’s Not Luck』(邦題:ザ・ゴール2)などの著者であるエリヤフ・ゴールドラット博士(Dr. Eliyahu Goldratt)によって提唱された理論です。ゴールドラットは物理学の博士号を持っており、物理学の考え方を組織社会・人間社会に適用した理論がTOCであると言うことができると思います。そのため、TOCは非常に科学的な手法となっています。また、TOCは、産業をはじめとして、サービス、政府・公共機関、教育、国防、医療など幅広い分野において大きな収益改善を実現してきています。
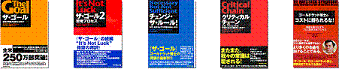
TOCの特徴の一つ目は、全体論的アプローチの採用により、企業全体の収益改善を妨げている制約条件を特定し解消することです。部分最適に陥ってしまうのではなく、工場や会社を一つの大きな「システム」(仕組み)としてとらえ、全体最適の観点から根本問題を解決しようとします。二つ目の特徴は、短期間で劇的な効果を実現する手法であると言うことができるでしょう。これまで我々がTOCの導入を支援した事例では、業務設計5週間と移行期間3週間の合計2ヶ月で本番し、導入後わずか1ヶ月で生産リードタイムの80%削減に成功したり、また、他の事例では、業務設計2ヶ月と移行期間3ヶ月の合計5ヶ月で本番し、生産管理方法の改善で営業利益を大幅に拡大したりしています。
3.TOCの改善手法とは…
TOCでは、組織(ある機能部門であったり会社全体であったり)のパフォーマンスを改善するにあたっては、どのような場合であっても以下のようなプロセスを適用します。
STEP1: 制約条件を特定する
STEP2: 制約条件を徹底的に活用する
STEP3: 制約条件以外を制約条件に従属させる
STEP4: 制約条件の能力を向上させる
STEP5: もし前のステップで制約条件が解消されているならばSTEP1に戻る
工場のみなさんであれば“制約条件”という言葉を“ボトルネック工程”に置き換えてみると分かりやすいかもしれません。多くの工場ではこのSTEP1~3までをきちんと実行すれば、先ほど申し上げたような大きな効果を出すことができますので、むやみに設備能力を向上させる必要はなくなります。STEP3までをきちんと実行してもまだ設備能力が市場需要を下回った時に初めて、設備投資することになります。したがって、設備投資が非常に限定的かつ効果的になります。
この“改善の5STEP”を活用して、次のような8つの分野のTOCソリューションが開発されています。TOCを導入するにあたっては、これらのTOCソリューションの中から最も効果的なものから適用していくことになります。
- ドラム・バッファ・ロープ(Drum-Buffer-Rope)
- 企業内サプライチェーン(Replenishment)
- 企業間サプライチェーン(External Replenishment)
- クリティカルチェーン・プロジェクトマネジメント(Critical Chain Project Management)
- セールス(6 Phases of Buy-in)
- 組織管理(Managing People)
- 全社戦略、機能戦略(Corporate, Business and Functional)
今回の連載では、一番上のドラム・バッファ・ロープ(Drum-Buffer-Rope)と呼ばれる、TOCによる生産革新手法を詳しく紹介しましょう。これは、ゴールドラットが書いた『ザ・ゴール』というビジネス小説の中でも紹介されている手法です。本稿を読み終えてTOCに興味を持たれた方には、ぜひ『ザ・ゴール』を読まれることをお勧めします。少し分厚いのですが、小説仕立てで非常に面白いので、あっという間に読めてしまいます。
4.生産を行進中の兵士にたとえると…
では、このTOCによる生産革新がどのような考え方なのかを紹介するにあたって、生産を行進中の兵士の隊列にたとえてみましょう。6つの工程からなる工場を想像してみてください。そうすると、先頭の兵士は投入工程に相当し、最後尾の兵士は出荷工程に相当します。隊列の長さは、仕掛りの量と読み替えることができますし、生産リードタイムは、先頭の兵士がある地点を通過してから最後尾の兵士がその地点を通過するまでの時間ということになります。
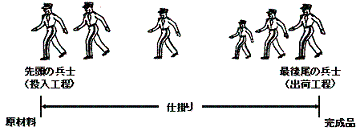
出典:Avraham Y. Goldratt Institute(AGI)の資料を元に作成
この隊列が長くなるということは、仕掛りが多くなることを意味しますし、隊列が短いということは、仕掛りが少ないことを意味します。それでは、一体どうすれば、行進全体のスピードを落とさずに隊列が長くなるのを防げるのでしょうか?別の言い方をすると、どうすれば、隊列をコンパクトに縮めながら速いスピードで行進できるのでしょうか?これを工場に置き換えてみると、どうすれば仕掛り量を少なく保ちつつ工場の生産のスピードを速くすることができるのかを考えることになります。
5.制約条件を特定しよう!
それでは、先ほどの“改善の5STEP”にしたがって、まずSTEP1(制約条件を特定する)として、この隊列における制約条件を見つけてみましょう。隊列の中で最も足が遅い兵士が行進全体のスピードを決めてしまいます。この最も遅い兵士が歩くスピード以上の速さで隊列は進むことができませんし、この最も遅い兵士が歩く距離以上に隊列は進むことができません。工場に置き換えてみると、最も能力が低い工程が処理するスピードよりも速く工場全体は生産することはできないし、最も能力が低い工程が処理する量よりも多くを工場全体は生産することはできないということになります。
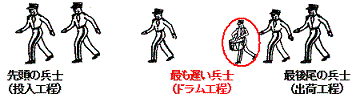
出典:Avraham Y. Goldratt Institute(AGI)の資料を元に作成
そこで、最も遅い兵士に太鼓(ドラム)を持たせて、最も遅い兵士のリズムに合わせて隊列全体が行進することにします。すなわち、最も能力が低い工程のスピード(ドラムのリズム)に合わせて工場全体が生産することになります。この最も能力が低い工程のことをドラム工程と呼ぶことにします。
6.制約条件は徹底的に活用しなくっちゃ!
次に、STEP2(制約条件を徹底的に活用する)では、最も遅い兵士が目一杯頑張ることができるようにしてあげましょう。行進全体のスピードを守るために、最も遅い兵士の前にゆとり(バッファ)を作ってあげます。前の3人の兵士のうちの誰かがこけたり、靴の紐を結んだりするために立ち止まっても、最も遅い兵士が歩き続けられるようにしてあげるのです。なぜなら、最も遅い兵士が一度失った距離は二度と取り戻せないので、彼は立ち止まることなく歩き続けなければならないのです(少しかわいそうですが...)。
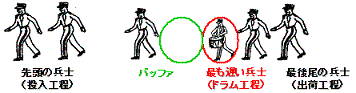
出典:Avraham Y. Goldratt Institute(AGI)の資料を元に作成
工場に置き換えてみると、ドラム工程の生産量が工場全体の生産量を決めてしまうので、ドラム工程を決して停機させてはいけません。そこで、前の工程がトラブルなどで停機したとしてもドラム工程が生産し続けられるように、ドラム工程の前だけには若干の仕掛りを置いておきましょうということなります。
7.制約条件以外を制約条件に従属させるって?
最後に、STEP3(制約条件以外を制約条件に従属させる)で、隊列の広がりを抑えるために、最も遅い兵士と先頭の兵士をロープで結びます。最も遅い兵士がドラムを叩いてリズムを行進全体に教えているのですが、前の兵士達は足が速いのでどうしても先に先に行ってしまいがちです。そこで、前に行ってしまい過ぎないようにロープで結んでしまうのです。その時は、ゆとり(バッファ)を持たせて、短過ぎず長過ぎない長さのロープで結んであげます。
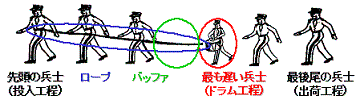
出典:Avraham Y. Goldratt Institute(AGI)の資料を元に作成
工場に置き換えてみると、ドラム工程よりも前の工程は、生産能力が高いのでついつい早め早めに原材料を投入して、仕掛りを作ってしまいがちです。そのため、早過ぎず遅過ぎないタイミングで原材料を投入するようにコントロールすることが重要になってきます。
8.そんなに上手くいくの?
このように、ドラム工程を特定して、バッファを置いて、ロープで結ぶことから、このTOCによる生産革新の手法をドラム・バッファ・ロープ(Drum-Buffer-Rope)と呼びます。英語の頭文字をとってDBRと略したりすることもあります。
今回のたとえ話は非常に簡単な例ですが、実際の工場はこんなに簡単じゃなく、工程数も多いし、工程の流れも複雑だし、製品数だって多いから、そんなに簡単にはいかないというご意見はよく頂戴します。それはその通りです。ただし、このTOC/DBRの基本的な考え方をもとに、各社各様にカスタマイズして導入していきます。TOC/DBRは非常に簡単な(シンプルな)考え方ですが、このような考え方をなかなか実践できてない工場が多いのではないでしょうか?それは、工程数が多かったり、工程の流れが複雑だったり、製品数が多かったりするだけが理由ではありません。
これまで、我々は電子部品、衣料、自動車部品、機械部品、半導体などの様々な工場へのTOC/DBRの導入を支援してまいりましたが、制約条件の95%は、物理的な制約(工程の能力が不足しているなど)ではなく、方針制約でした。すなわち、自分たちの誤った方針や考え方が、ボトルネックではない工程を勝手にボトルネックにしたり、生産リードタイムを不用意に長くしたりしてしまっていたのです。TOC/DBRでは、考え方や方針を変えることにより、短期間に大きな改善を得ることができます。我々の経験では、生産リードタイム短縮や仕掛り削減で5割以上の改善も珍しくありません。
冒頭に述べました、生産管理を難しくしている10個の原因に対して、TOC/DBR導入による一般的な定性的効果としては次のようなものが挙げられます。
- 生産リードタイムの極小化
- 仕掛り量の削減と仕掛りポイントの絞込み
- 工場の生産能力の向上
- 納期遵守率の向上
- 完成品・原材料の在庫レベルの適正化
- 生産の管理ポイントの明確化
- 計画の見える化
- 納期回答の精度の高度化
- 継続的改善の効率化
これらすべての効果が、あらゆる工場で達成できるとは申しません。どのような効果がどの程度の大きさになるかは、その工場がどのような問題を抱え、その問題がどの程度の大きさかということに依存します。通常、我々は、工場を見学し、想定効果を見積もった上で、TOC/DBRを導入すべきかどうかをご提言しております。
それでは、次回は、TOC/DBR導入による代表的な効果である、生産リードタイムの極小化と、仕掛り量の削減について、どのようなメカニズムでその効果が出るのかといったあたりを、事例も交えながらもう少し掘り下げていきましょう。
第1回:どうして生産管理は難しいの?
第2回:生産リードタイムはどこまで短くできるのだろう?
第3回:設備投資なしで生産能力が増えるってホント?
第4回:TOCとJITって仲良し?仲悪い?
以 上