RIM 環太平洋ビジネス情報 1998年10月No.43
新たな動きをみせる日系自動車部品メーカーのアセアン戦略
1998年10月01日 さくら総合研究所 森美奈子
はじめに
アセアン4カ国(タイ、マレーシア、インドネシア、フィリピン)の自動車市場は、80年代末より、経済成長を背景に急速に拡大した。86年には4カ国合わせて31万台に過ぎなかった自動車販売台数は、96年には145万台へと4.7倍に増加し、2000年に向けて順調に伸びていくものと見込まれていた(図1)。しかしながら、97年7月の通貨危機の発生とその後の政治・経済の混迷によって市場の様相は一変し、低迷が長期化している。
本稿では、アセアンの自動車産業の状況を、日系一次部品メーカーの対応を中心に述べる。部品メーカーは、通貨危機に見舞われる直前までアセアンへの新規進出や生産能力の増強を加速させていたため、状況は厳しいが、輸出に取り組むなど新たな動きをみせている。裾野の広い自動車産業の基盤を支える一次部品メーカーがどのような戦略を展開するかは、今後のアセアンの自動車産業を展望する上での重要なポイントとなろう。
I.厳しさを増す自動車産業をめぐる環境
1.低迷続く自動車市場
通貨危機が発生して以来、アセアンの自動車市場は急速に縮小した。国により状況は異なるが、97年第4四半期より、4カ国とも月間販売台数が前年同月の水準を割り込むようになり、98年に入っても低迷が続いている(図2)。
アセアンの月間自動車販売台数
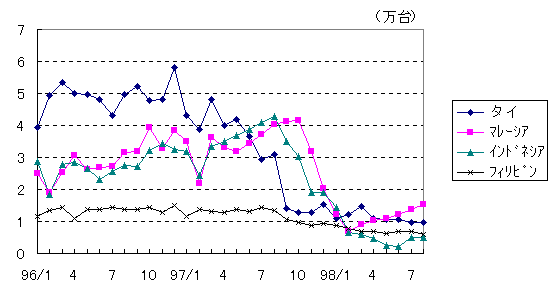
97年7月に最初に通貨危機に見舞われたタイの自動車販売台数は、97年初頭から商用車の販売不振により伸び悩んでいたが、9月以降、急速に落ち込んだ。この結果、97年の年間販売台数は36万台と、史上最高の59万台を記録した96年に比べ、23万台もの減少となった。98年に入ると、市場は一段と冷え込み、1~8月の累計販売台数は9万台と、前年同期比71%のマイナスとなった。特に7月と8月の月間販売台数は、乗用車の減少によって1万台を割り込んだ。
マレーシアでは、97年の販売台数は前年比14%増加し、40万台を超えた。しかし、97年11月を境に市場は冷え込み、98年1~8月では前年同期比66.4%減の9万台となった。同国では、従来から乗用車、とりわけ国民車の市場シェアが高かったが、98年以降、価格の安い国民車への集中度が一層高まり、商用車および国民車以外の乗用車の落ち込みが著しい。このため、販売台数に占める乗用車のシェアは、97年の76%から98年8月には89%に高まるとともに、乗用車に占める国民車のシェアは、同じ期間に82%から93%まで上昇した。
インドネシアは、97年については、年前半に低価格車や新型車の投入で販売が好調だったことから、通年で過去最高の39万台に達した。しかし97年10月以降、政治の不安定化と経済の混迷により、販売台数が前年同月を下回るようになった。とりわけ98年5月および6月には、暴動やスハルト大統領の退陣など、政治の混乱が続いたことから、月間販売台数は2,000台レベルまで急減した。
フィリピンは、98年1~8月で前年同期比47%減と、アセアンの中では下落幅が小さいものの、販売台数は5.6万台にとどまっている。
こうした市場縮小の要因として、第一に景気の悪化による消費の低迷がある。第二に、輸入関税の引き上げと通貨下落による輸入原材料コストの上昇を受けて、完成車の販売価格が引き上げられたことが挙げられる。国によっては、付加価値税など内国税の税率も引き上げられ、自動車購入にかかる費用負担はますます大きくなっている。
また、金融システムの混乱に伴い、オートローンの取り扱いが減少していることも見逃せない。例えば、タイでは通常、自動車購入者の7割が自動車ローンを利用していたが、現在では4割に減少しているという。ローン会社が資金不足で、ローンを提供できないことがその背景にある。他方、マレーシアでは、金融引き締め策の一環として一時強化されていた自動車ローン規制が、98年5月、7月の2回にわたって緩和された。これにより、返済期限が撤廃されるとともに、ローン利用の上限は自動車価格の70%から85%に引き上げられた。こうした措置を受けて、マレーシアの販売台数は4月以降、前月比ではやや上向いているが、本格的な回復には至っていない。
2.事業計画の修正を余儀なくされる完成車メーカー
このようにアセアンの自動車市場が冷え込むなか、自動車組み立てメーカー(以下、完成車メーカー)は、事業計画の大幅修正を余儀なくされた。特に97年第4四半期から98年前半にかけては、在庫調整のため、操業を一定期間停止する企業が多数みられた。現在は多くの企業が操業を再開させているものの、生産規模は非常に小さい。とりわけ近年、各社は生産能力を増強させてきたため、稼働率が著しく低下している。例えば、タイの98年8月の生産実績は1.6万台だが、これは同国の自動車生産能力からみると、23%という低水準の稼働率である。
通貨危機前に計画していた投資や新型車の販売も延期されている。日産自動車はインドネシアでのエンジン工場建設計画を凍結、日野自動車工業もインドネシアでのトラック工場の建設を延期した。年産23万台と、アセアン最大の生産能力を持つマレーシアの国民車メーカーのプロトンも、第2工場および研究・開発センターや住宅を併設する「プロトン・シティ」の建設を延期した。98年の生産目標も、前年実績の23.6万台から12万台(輸出分5.2万台を含む)に引き下げた(98年6月時点)。
タイでは98年に、マツダとフォードの合弁会社であるオート・アライアンス・タイランド(AAT)およびGMが、年産10万台規模で生産を開始する計画であったが、両社とも計画を変更した。AATは、98年7月に操業を開始したが、国内需要が落ち込んでいるため、輸出比率を高めるとともに、当初予定より生産台数を大幅に抑えている。一方、GMは、98年6月に、操業を2000年に延期すると発表した。生産車種もセダンからミニバンに変更するとともに、生産台数も当初計画の10万台から4~6万台に縮小するという(98年6月8日付け「Bangkok Post」紙)。
国内販売が急減する中で、完成車メーカーはアセアンからの輸出に活路を見いだそうとしている(表1)。完成車メーカーの輸出は、完成車の輸出と部品の輸出とに大別できる。部品輸出は、完成車メーカーが所有する部品工場からの輸出(エンジンやトランスミッションなど)に加えて、現地部品メーカー支援のため、現地調達部品を輸出する動きもみられる。
現在、完成車輸出の実績が最も多いのは、タイの三菱自動車工業である。同社は、すでに96年よりタイをピックアップトラックの輸出拠点と位置づけており、97年央以降のタイ・バーツ安を追い風に、輸出を拡大させている。98年1~7月の輸出は、前年同期比1.6倍の約3万台に達した。欧州向けピックアップトラック輸出が好調で、さらに7月よりニュージーランド向け乗用車輸出を開始したことから、同社は98年のタイからの輸出を、前年比2万台上乗せし、6万台とする計画である。
また、98年9月以降、他の日系企業も完成車輸出を開始する。トヨタ自動車は、10月より年間2万台を目標に、タイ製ピックアップトラックをオーストラリア、ニュージーランドに輸出する。また、インドネシアで生産している商用車「キジャン」の輸出も拡大する方針である。一方、本田技研工業(以下、ホンダ)は、タイから、アジア戦略車「シティ」を98年9月より中近東へ輸出するのに加え、12月より乗用車「アコード」をオーストラリアとニュージーランドに年間6,000台を目標に輸出する計画である。日産も、99年よりタイ製ピックアップトラックを輸出する。
しかしながら、現在のところ、アセアンからの完成車輸出台数は、各国の生産能力に比べると非常に小さい。タイにおいても、1~7月の累計で3万559台に過ぎず、国内市場の不振をカバーするには程遠い状況である。
3.日系企業への影響-タイの事例
アセアンの自動車・部品産業は、通貨危機とその後の経済低迷の影響を大きく受けた代表的な業種であり、多くの日系企業で経営が悪化している。これは、日系完成車・部品メーカーが、各国の国産化政策を背景に、国内市場をターゲットとしてきたという特性を持つためで、輸出志向の労働集約型産業やエレクトロニクス産業とは状況が異なっている。
ここでは、日系完成車・部品メーカーが最も集積しているタイを例に、日系企業の状況をみてみたい(表2)。バンコク日本人商工会議所が98年5~6月に会員企業を対象に行ったアンケート調査によると、完成車・部品メーカーを含む輸送用機械業種の売上高は、通貨危機発生により、97年以降大きく変化した。売り上げが増加している企業の割合は、96年には63%(12社)であったのに対し、97年には20%(6社)に減少している。また、97年の売上高を製造業全体と比較すると、輸送用機械では前年度より減少している企業の割合が70%(21社)と、製造業全体の32%(64社)に比べ、きわめて高い。98年度の売上高の見通しについても、輸送用機械では77%(23社)の企業が減少すると回答しており状況はさらに悪化している。
経常利益をみると、輸送用機械業種は、97、98年度とも赤字の企業が60%を超えている(19社)。製造業全体では、98年度の赤字企業の比率は前年度の51%から30%へと減少していることから、輸送用機械業種の状況が厳しいことがうかがえる。しかしながら、輸送用機械業種においても、98年度には利益が拡大する(黒字拡大のほか、赤字縮小、赤字から収支均衡を含む)と回答している企業が前年度の3%(1社)から33%(10社)に増加し、利益がさらに縮小すると回答している企業が97%(28社)から53%(16社)へと減少している。状況は厳しいが、後述のように各社がコスト削減などの対応を講じていることがうかがえる結果となっている。
II.日系自動車部品メーカーの対応
1.日系メーカーの集積が進展していたアセアン
ここではまず、通貨危機発生前までの日系自動車部品メーカーの動向を整理しておきたい。94年から96年までの間は、日本の部品メーカーのアセアン進出が急速に進んだ時期である(表3)。とりわけタイへの集中が著しく、96年の40件をピークに、94年から97年にかけて100件以上の進出がみられた。
この背景には、90年代のアセアン市場の急成長を受けて、日系完成車メーカーが生産能力の増強と新型モデルの投入を計画するとともに、生産コスト削減のための現地(アセアン域内を含む)調達を進めていたことがある。また前述の通り、マツダ・フォードの合弁会社やGMの操業も予定されていた。部品メーカーは、こうした完成車メーカーの動きに対応して、新規進出や生産能力の拡充を行っていた。特に94年以降、二次部品メーカーの進出もみられるようになり、アセアンの部品産業の裾野が広がりつつあった。表4は、96年2月に行ったアセアンの日系完成車メーカーに対するアンケート調査の中で「現在は現地または域内調達できないが、2~3年以内に現地・域内調達が可能」と回答した企業の比率が高い部品を抽出したものである。ディスクブレーキ、ステアリングリンク、コンビネーションスイッチ、ドライブシャフト、コンビネーションメーターについては、アセアンに拠点を持つ企業のうちの約半数が、98~99年までに現地または域内の部品メーカーから購入する計画を持っていたことになる。
2.通貨危機の影響
このように部品メーカーのアセアンへの集積が急速に進んでいた時期に、通貨危機が発生し、市場が急激に冷え込んだ。部品メーカーへの影響は、次の3点にまとめられる。
第一に、大幅な生産調整や投資計画の変更を強いられていることである。国内市場の成長を背景に、多くの企業はアセアンの拠点を、当該国内ないしは域内への供給拠点として位置づけてきたことから、市場低迷の影響を大きく受けている。なかには、工場の稼働率が従来の約3分の1に落ち込んでいる企業もある。特に、94年から96年にかけて進出した企業は、生産が本格化する時期に市場縮小に見舞われた。また、97年から98年にかけて予定されていた新型車の発売計画の多くが延期されたため、部品メーカーの間には、設備投資を中断したり、完成した工場の稼動時期を遅らせるなどの動きがみられる。このほか、地場企業への技術供与契約が終了するのを機に、資本参加による合弁会社設立を計画していたが、計画を延期し、再度技術供与にとどめた企業もある。
第二に、現地通貨の下落によって部品、原材料の輸入コストが高騰し、生産コストの上昇を招いていることである。日本自動車部品工業会の調査によると、日系部品メーカーのアセアンでの現地調達率は56.4%(97年4月時点)で、欧米や他のアジア地域に比べて低い。現地の部品・裾野産業が未熟であるために、部品、原材料を日本からの輸入に依存している割合が高い。現地で調達している部品であっても、その原材料であるアルミ、鉄鋼などのうち特殊な高付加価値品は、日本から輸入しているのが実状である。
第三は、為替下落による財務内容の悪化である。為替下落によって、外貨建て債務の返済負担が増大している企業が多い。また、合弁企業の場合は、合弁相手の地場企業の資金力が低下しているケースも多くみられる。加えて、日系部品メーカーに部品や原材料を納入している地場サプライヤーの状況も深刻である。現地金融機関の信用供給力の低下や高金利のため、資金繰りが悪化している企業もある。日系部品メーカーにとっては、安定した部品供給が受けられなくなる、地場企業の先行きが不透明で技術移転ができなくなるなど、地場企業の経営悪化が調達戦略に影響を及ぼすことが懸念される。
3.生産拠点維持に取り組む日系部品メーカー
こうしたなか、日本企業はアセアン拠点の操業を維持するために、さまざまな対策を実施している。これは、各社がアセアン市場の長期的な成長力を重要視しているためである。また、ひとたび工場を閉鎖すると、これまで育成してきた人的資源を失ううえ、生産設備のメンテナンスの面からも生産再開は容易ではないことも一因である。
部品メーカーの主な対応策は、以下の3点にまとめられる。
第一に、輸出の取り組みを積極化させていることである。加えて、完成車メーカーも、日本や第三国でアセアン製部品を採用し始めた。このように、完成車・部品メーカーが協力して、現地拠点の操業維持に努めている。アセアンからの輸出は、今回の対策を特徴づけるものであり、今後のアセアン戦略にも影響を及ぼすものと考えられるので、次節で詳述する。
第二に、コスト削減に取り組んでいることである。為替レートの下落による輸入原材料価格の高騰を受けて、各社は納入先との協議のうえ、製品の納入価格を引き上げた。しかし、市場低迷の折に、生産量の減少と為替の下落とに見合った価格転嫁は難しく、各社は内部努力によるコスト削減に取り組んでいる。
まず、部品、原材料の現地調達の拡大である。日系部品メーカーは、これまでも現地調達を進めてきたが、今回の通貨危機によって、為替変動に左右されにくい生産体制を築くことが一層重要な課題となり、取り組みを加速させている。例えばデンソーは、タイで97年に新たに200点の部品を現地調達した。98年には、調達品目をさらに220品目増やす計画である。こうした取り組みによって、現在50%の現地調達率を、99年までに65%にするという。
また、リストラによるコスト削減も進展している。現地従業員の削減のほか、同一国内に複数の工場を持っている企業の場合、工場を集約する動きもある。このほか、日本から専門家を派遣し、生産管理や品質の向上を図る企業もある。
第三に、アセアン拠点に対し、日本本社が金融支援を行っていることである。最も多くみられるのが増資である。合弁企業の場合、日本企業側が増資額の多くを引き受け、為替下落により増大した債務返済に充てるなど、財務基盤を強化している。とりわけタイでは、97年12月に外国資本出資比率規制の緩和が公示され、日本企業による増資引き受けが活発化している。タイの投資委員会によると、97年12月から98年7月までに外国資本が追加出資した138件のうち、輸送機器分野は45件に達している。その多くが日本企業によるものと推定される。また、日本本社から現地企業に融資する例もみられる。
4.拡大するアセアン拠点からの部品輸出
98年に入り、部品メーカーの輸出計画が相次いで発表、実現されている。労働集約的な部品については、93年以降の円高時にアセアンを輸出基地化している企業もあった。しかし、最近の輸出への取り組みの特徴は、輸出を行う企業数が多い上に、輸出用製品の生産によって現地拠点の稼動率を引き上げるという、「支援」の色合いが強いことである。このため、日本向けの輸出、つまり日本からみると「逆輸入」が大半である。一方、完成車メーカーも、部品調達ネットワークなどアセアンでの生産基盤を維持するために、アセアン製部品を日本や米国で採用し、サプライヤーを支援している。
(1) 貿易統計からみたアセアン製品の逆輸入の変化
ここでは、日本の貿易統計を用いて98年1~7月(以下、98年)と前年同期(以下、97年)の輸入額を比較することで、通貨危機発生以降、日本においてアセアンからの自動車部品(以下、部品)輸入が進展しているかを検証してみたい。
2時点の輸入額を比較すると、大きく増加しているのはタイのみで、その他の国は減少ないし横ばいにとどまっている(図3)。いい換えれば、アセアンからの逆輸入は、タイ製品について集中的に行われている。これは、タイが(1)アセアンの中で最も部品メーカーが集積していること、(2)アセアンで最初に通貨危機が発生し、市場が落ち込んだため、日本企業が他の拠点に先駆けて対応策を採ったこと、が理由と考えられる。98年に輸入額が前年同期比1億円以上増えた品目を抽出してみても、タイが突出している(図4)。タイからの輸入増加額が最も大きい部品はタイヤで、2.8億円から20.8億円へと7.4倍に拡大した。第2位の内燃機関・部品は、ディーゼルエンジンおよびエンジン部品の逆輸入の増加による。第3位の車輪・同部品・付属品は、2,000万円から12億円へと著しい伸びをみせた。このほか、97年には輸入がほとんどみられなかったが98年に輸入が大きく伸びている部品としては、鉄鋼製のばね(2,000万円→3.5億円)、ハンドル・ステアリングコラム・ステアリングボックス(100万円→1.5億円)、デファレンシャル付き駆動軸(20万円→8,000万円)などがある。
図3 日本のアセアンからの自動車部品輸入
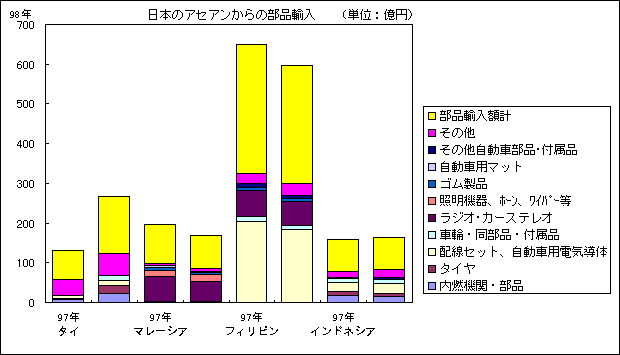
他の3カ国については、通貨危機前後で輸入品目の構成にそれほど大きな変化はみられない。フィリピンは従来より、低コストを生かしたワイヤーハーネスやカーラジオの輸出拠点と位置づけられ、日本の部品輸入相手国としてはアセアン最大である。特に、ワイヤーハーネスが含まれる配線セット・自動車用電気導体では、日本の輸入総額の42%のシェアを占める。マレーシアは、ラジオ、カーステレオ、照明機器、ホーン、ワイパーなどといったエレクトロニクス部品の比率が高い。インドネシアについては、輸入額1位の配線セット・自動車用電気導体、同2位の内燃機関・部品、同4位のタイヤの金額が減少し、輸入総額も横ばいである。インドネシア市場が混迷を深めているため、同国からの逆輸入は今後の課題となろう。ただし、タイに比べ裾野産業が未熟であるうえ、先行するタイからの逆輸入品目といかに棲み分けるかなど、解決すべき点は多い。
(2) 活発化する日本企業の輸出の取り組み
日本企業のアセアンからの輸出の取り組みは、企業の事例に基づいて、以下の3つに分類できる。
1) 対日輸出
表5は、日系部品メーカーの主な部品輸出の取り組みをまとめたものであるが、そのほとんどが日本向けである。こうした日本向け輸出のパターンの第一は、日本と仕様が同じ部品を抽出し、アセアンからの輸出に切り替えるケースである。新規投資は極力抑え、アセアンの生産設備を活用しようとするものである。第二は、日本で生産している部品の生産を新たにアセアンに移管し、日本に輸出する例である。これは、生産品目を増やすことで現地の稼働率を引き上げるもので、場合によっては設備投資を必要とする。このほか、日本から部品などを送り、現地で機械加工などを行った後、日本に持ち帰るといった工程の一部をアセアンで行うケースもある。
こうした事例の大半は、日本での生産分の一部をアセアンからの輸入に切り替えたものであるが、日本での生産を停止し、すべてアセアンからの輸入とした企業もある。ミツバは、IC式フラッシャーリレーの生産を日本からタイに全面移管した(98年4月6日付け「日経産業新聞」)。
2) 海外拠点間での分業
複数の海外拠点を持つ企業の場合、他の海外拠点も交えた分業によって、アセアン拠点を支援している。ユニシア・ジェックスは、パワーステアリング・ポンプをタイから台湾へ輸出している。従来は、自社の台湾拠点から、台湾にある完成車メーカーへ納入していたが、生産量の一部をタイにシフトし、タイから台湾への輸出に切り替えた。また、豊田合成は、日本から台湾に輸出していたハンドル芯材と、米国拠点が日本へ輸出していた革巻きハンドルの生産をタイに移管し、タイからの輸出に切り替えた。日本からタイへの生産シフトにあたっては、日本から生産設備を移し、アルミ加工を行えるようにした。同社のタイ拠点は、これまで鉄製の芯材を生産していたが、これを機に国内市場向けもアルミ製芯材に切り替えていくという(98年6月9日付け「日刊工業新聞」)。
3) 完成車メーカーのアセアン部品の採用
日本の完成車メーカーも、部品メーカー支援のため、アセアン製部品を日本や米国の組み立て工場で採用し始めた(前出表1)。三菱自工は、米国で生産する「ギャラン」の部品や、日本で生産する「ランサー」の部品をタイから輸入すると発表した。ホンダも、日本で生産している米国向け「アコード」の部品をタイとマレーシアから調達している。また、98年内に欧州でも、アルミホイールなどタイ製部品を採用する計画という。この他の企業も、アセアンから調達可能な製品の洗い出しを進めている。
(3) 輸出に際しての問題点
このように、部品メーカーは輸出拡大に取り組んでいるが、もともとアセアンが現地・域内向け生産拠点であったことから、輸出に際して問題点がいくつか指摘できる。
第一に、現状ではアセアンから輸出できる品目が限定されることである。アセアンでは、域内仕様に対応する生産設備を導入しているために、輸出仕様の製品を生産できないケースもある。例えば、輸出自動車用のカーエアコンには、アセアン仕様にはない暖房装備が必要であるが、ある企業は、既存生産設備では生産できないため、輸出車用のエアコン部品は日本から輸入しているという。一方、新しい設備を導入するには、設備投資に見合う生産量を確保しなければならず、販売先の開拓や他の生産拠点との調整が必要となろう。
第二に、輸出が実現するまでに時間がかかることである。実際に製品が輸出されるようになったのは、通貨危機発生から半年以上を経た98年に入ってからが多い。輸出部品の選定や生産の準備作業もさることながら、その部品についての社内および納入先における検査・承認に時間を要したためという。
第三に、アセアンからの輸出製品は、必ずしも国際競争力を持たない場合もある。日本向け輸出が主流であることからも明らかなように、アセアン製部品を採用するために、自社の内外拠点の生産量もしくは国内のサプライヤーへの発注量を調整している企業が大半である。また、アセアン以外の海外拠点において、当初進めていた現地生産計画を一時中断させて、アセアン製品を輸入している例もある。このほか、現地ないし日本本社の支援を背景に、赤字価格で輸出している例もあるという。
III.自動車市場の展望とわが国部品メーカーの課題
1.自動車市場の展望と完成車メーカーの動向
アセアンでは経済の低迷が続いており、98年6~7月時点における各国の自動車工業会の予測では、98年の販売台数は42.5万台(表6)と、前年の3分の1の水準に落ち込むとみられる。これは、80年代末の市場規模に相当する。また、7月以降も市場に回復の兆しがみられないため、予測が下方修正される国もある。タイでは、98年の販売台数は15万台を下回るとの見方が大勢を占め、99年は10万台へとさらに悪化するとの声も聞かれる。買い替え需要などにより、市場はまもなく底を打つであろうが、通貨危機直前のピーク時のレベル時に回復するまでには、しばらく時間がかかるとの見方が多い。
しかしながら、アセアンは中長期的には高い成長力を持つ市場として期待されている。このため、日系完成車・部品メーカーの多くは、回復期に備えて、部品調達も含めた生産基盤を維持するために、アセアンへの支援を続けていくことになろう。
日系完成車メーカーは、輸出で一定の生産量を確保するにしても、引き続き国内向け生産が事業活動の中心となろう。完成車輸出に際しては、輸出先の安全・環境基準に合う仕様に変更する必要があるが、現在のアセアンの生産体制では限界があるためである。このため、日系完成車メーカーの輸出先はほとんどの場合、生産設備の制約によって、右ハンドルのオセアニアや近隣アジア諸国など、比較的仕様の変更が少ない国に限定されている。また、アセアン諸国は完成車の輸入関税が高いため、域内輸出を大きく拡大させることも難しい。
こうしたことから、小さい国内市場をめぐる完成車メーカー間の販売競争は一層厳しくなろう。現在、完成車メーカーは、ディーラーやオートローン子会社の支援、販売キャンペーンの実施、アフターサービスの強化などを行っているが、このような動きはさらに強まろう。また、新型車の投入もみられるようになった。投入車種は、乗用車に比べて低価格で、乗用・商用など幅広いニーズに対応できるピックアップトラックや多目的車が多い。特にタイでは、7月から9月にかけて4社が相次いで新型ピックアップトラックを投入した。また、市場確保のため値引きが行われるなど、競争が激化している。
完成車メーカーは、生産面ではコスト低減のため、部品の現地・域内調達を推進するが、その一方で現地・域内調達の効率化のため、調達先の絞り込みを加速させるものと思われる。94年以降の進出ラッシュによって部品メーカーが集積してきた現在、部品メーカーにとっても競争がますます厳しくなることが予想される。
2.通貨危機により明らかになった日本の部品メーカーの課題
アセアンにおいて、日本の部品メーカーは、完成車メーカーとともに、国産化政策に対応しながら現地の技術レベルや市場特性に合った製品を開発するなど、現地に密着した努力を重ねることで生産基盤を築いてきた。アジア戦略車はその好例である。現地で生産しやすく、かつアジアに不要な装備を省くといった設計・開発面の工夫によって、低価格を実現し、購買層を拡大してきた。そして、こうした生産体制がアセアンの自動車産業の発展を支えてきたといえる。
しかしながら、市場の低迷が長期化するにつれて、こうした生産体制に内在する課題も明らかになったように思われる。アセアンにおいても、国内市場や為替相場の変動の影響を受けにくい生産体制の構築が求められている。そのためには、中長期的な観点から、アセアンの拠点をいかに位置づけるかを再考する必要があろう。生産品目によって多少の違いはあろうが、今後、アセアンにおける日系一次部品メーカーの検討すべき課題として、以下の3点を挙げたい。
(1) 輸出機能の強化
第一に、アセアン域外への輸出が可能な体制を整えることである。一定割合を輸出に振り向けることで、内需縮小による生産面でのリスクが軽減されることに加え、外貨バランスが改善され、為替変動をある程度カバーすることが可能になる。例えば、タイでランプを生産するスタンレー電気は、米国や日本向けの輸出を拡大し、輸出比率を現在の5%から、2001年~2003年には30%に引き上げる方針である(98年7月27日付け「日刊工業新聞)。また、日本に比べ、低コストで生産できる部品については、コスト競争を武器にすることができる。ゼクセルは、ボルボへのカーエアコン用コンプレッサーの輸出を、日本からタイに切り替えることを決定した。これは、ボルボが部品調達先を分散化する戦略であったことに加えて、タイ製部品が日本製に比べ、10%低コストであったためという。タイ拠点から日本にある完成車メーカーへの輸出が決定したある企業は、日本ではその企業への納入実績がなかったが、タイ製部品のコスト競争力によって新規受注を獲得したという。
通貨危機発生から1年を経た98年7月以降、アセアンへの投資を再開する企業もいくつかみられるようになった。こうした企業は、当初計画より生産量をかなり縮小しているが、現地での受注確保に加えて、輸出を行うことで、採算のめどをつけている。量産効果が期待できる装置産業的な部品の場合は、輸出機能を大幅に強化している。例えば、タイヤメーカーは、アセアンを欧米などへの輸出拠点と位置づけて、投資再開や新規投資に踏み切った。ブリヂストンは、欧米や日本向け輸出を織り込んで、インドネシアおよびタイの工場建設を再開した。横浜ゴムも、欧州向けをにらんで、フィリピン拠点の生産能力増強を決定した。
ただし、アセアンからの輸出に際しては、日本および他の海外生産拠点との棲み分けや、日本国内のサプライヤーへの影響について、十分考慮しなければならないだろう。現在のところ、アセアンからの輸出は支援的要素が強いが、今後、アセアンの生産レベルが向上し、競争力がつけば、恒常的にアセアンからの輸出に切り替える企業も出てこよう。このように、今回の通貨危機を機に、アセアンと日本における生産分業構造が、部分的にせよ変化する可能性もある。その一方、日本市場が成熟段階を迎えていることから、日本国内の生産体制との調整が課題となる。
(2) アセアン拠点の機能の見直し
アセアンでの生産拠点の機能を見直し、アジアの中核拠点としての機能を持たせたり、統括拠点の設置・活用によりアセアン事業の効率化を図ることも、検討すべき点である。こうした取り組みは、一部の企業では通貨危機前から行われていた。しかし、市場が縮小している現在、域内ないしアジア市場をカバーすることで部品産業に必要なスケールメリットが確保できること、また生産の効率化によってコスト削減やリスク回避が可能となることなどから、その重要性は高まっているといえる。
1) 中核拠点の育成
アセアンの1拠点を、アジア地域の中心的な拠点として位置づけ、機能を強化するという考え方もある。そのために、設計・開発機能、品質評価機能、金型生産機能などを日本本社から移管し、アセアン拠点の自立性を高めることが必要であろう。例えば、スタンレー電気は、タイをアジアの中核工場として、インドやベトナムにある同社の拠点へ金型や部品を供給していく方針である。同社のタイ拠点は、金型工場やR&Dセンターを有し、自動車ランプの一貫生産機能を持っている。小糸製作所も、2000年をめどに、タイに金型生産機能を移管することを決定した。将来的には、日本やインドへの金型輸出拠点として位置づける構想である。
2) 域内統括拠点の活用
アセアンに複数の生産拠点を持つ企業の場合、域内統括拠点を設置し、域内生産体制の効率化を図ることも考えられる。自動車市場が右肩上がりの成長を続けていた96年までは、各拠点が国内需要への対応に追われ、域内補完や、域内での集中管理に対する関心は薄くなりがちであった。しかし、通貨危機を機に、アセアン各拠点の原材料・部品の調達、マーケティング、為替管理などを域内統括拠点で集中的に行い、リスクの軽減や生産体制の効率化を図ることの重要性が高まっている。完成車メーカーやエレクトロニクスメーカーの間では地域統括拠点の設置がみられるが、一次部品メーカーも、こうしたロジスティックス面での効率化が必要となるだろう。
(3) グローバルな生産体制構築への対応
アセアンから目を転じて、自動車業界のグローバル化の流れの中でアジアを位置づけることも必要である。現在、部品メーカーには、完成車メーカーの世界戦略に対応し、グローバルな部品供給体制を構築することが求められている。GMのワールドカーへの納入を目指すある企業は、GMの拠点展開に合わせ、日、米、欧、アジアの4地域での生産拠点の整備を進めている。この企業は、タイをアジアの拠点と位置づけて、タイでも他拠点と同品質の部品を供給できるように生産準備を進めている。
一方、現在加速している日本と欧米の部品メーカーの提携においても、日本企業のアジア拠点は重要な生産基地となろう。日本を含むアジアでは日本企業の生産拠点を、欧米では提携先の拠点を活用することで、完成車メーカーの求める世界規模での供給を行うことが可能となろう。また、欧米メーカーとの提携の中で、アジア拠点を日本の生産基地として活用する構想を持つ企業もある。イズミ工業は、ドイツのマーレ社と提携し、マーレ社経由で欧米にエンジン用ピストンを輸出することを決定した。イズミ工業は、このピストンの生産の一部を、タイやインドネシアの拠点に移管することも検討しているという(98年8月13日付け「日刊工業新聞」)。
おわりに
現在、日系部品メーカーのアセアン拠点では、通貨危機対策として決定された輸出計画が実施段階を迎え、稼働率も一時期に比べ、持ち直している模様である。しかし、アセアンからの輸出を本格化させるには、品質、コスト、納期などの競争力の一層の強化が求められる。特に、品質面では、自社内の品質管理はもちろんのこと、サプライヤーを含めた品質管理の徹底が必要である。こうした観点からみると、(1)生産激減という危機意識から、地場サプライヤーの品質に対する意識が高まっていること、(2)アセアン支援のため、付加価値の高い製品の生産移管が進んでいることの2点は、長期的にアセアンの部品産業の競争力向上に寄与すると考えられる。
また、納入先である完成車メーカーのアセアン戦略の行方も注目される。アセアンのすべての拠点を維持する企業もあれば、日米欧と並ぶ世界の4極の1つとして、1カ国に集中的に支援・投資する企業も現れよう。いずれにせよ、生産拠点の維持を図る完成車メーカーは、現地の生産基盤を維持するため、日系部品メーカーと協力しながら、今後さらに支援を積極化させるだろう。その一方で、市場低迷が長引くと、生産拠点の再編・撤退を検討する企業が出てくる可能性も否定できない。こうした完成車メーカーの動向が、これまで以上に部品メーカーに影響を与えることになろう。
日系一次部品メーカーは、アセアンの自動車部品産業を支える要であり、その生産基盤が弱体化すれば、完成車メーカーのみならず、自動車産業全体に影響が及ぶことにもなりかねない。また、アセアンの自動車産業の国際競争力向上のためにも、今後、部品メーカーの果たす役割はますます重要である。現在、アセアンは市場回復を待つ持久戦ともいえる厳しい状況であるが、通貨危機後の日系部品メーカーの一連の取り組みは、各社のアセアン戦略の変化の契機となっていくものと思われる。